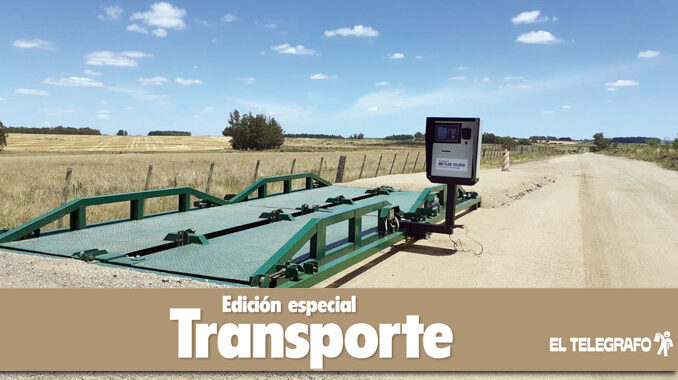
El transporte de cargas depende mucho de los sistemas de control de peso para su tránsito por las rutas uruguayas. Hay cuatro fuertes razones para este control: evitar las multas y eventuales trámites burocráticos por estar excedido de peso; tener un claro detalle de las cargas que se transportan, pero también por el cuidado de la mecánica del camión y los pavimentos en las rutas.
Acompañando el desarrollo del transporte de cargas, se complementó con la mejora tecnológica en las balanzas, que también se multiplicaron en las terminales de carga. En esa línea, lo que antes era una empresa puramente metalúrgica, ahora presenta una faz tecnológica, donde hay unas 20 personas vinculadas al emprendimiento, que también tiene presencia en Montevideo y Asunción del Paraguay.
El origen de la empresa, en 2008, fue para el desarrollo de la metalúrgica e instrumentación, pasando ahora a utilizar la tecnología que por ejemplo les permite, con mano de obra sanducera, exportar tableros que están trabajando en el Chaco paraguayo,
“Vinculados al transporte, estamos dedicados a fabricar e instalar balanzas de camiones. Y ya no se trata solo de pesar el vehículos y su carga, sino brindar la información a los clientes en línea y además también la posibilidad de hacer control y mantenimiento de los equipos en línea”, dijo José María Russi, explicando que “hoy podemos ver lo que está sucediendo con una balanza de camiones en Colonia, Cerro Largo o Montevideo, porque la tecnología que instalamos en pesaje permite hacer un mantenimiento preventivo de esos equipos en el marco de la llamada industria 4.0, porque tenemos el acceso para ello a través de la red, y podemos ayudar a tener una operación las 24 horas los siete días de la semana (24/7) como requieren hoy las agroindustrias, sin parar la operativa evitando esos costos, y eso favorece a la industria en general”.
Exportando trabajo sanducero
Sobre el desarrollo de la tecnología en los pesajes, Russi dijo que “desarrollamos sistemas que, por ejemplo, nuestra empresa instaló sistemas en Paraguay y podemos acceder a sistemas de embolsado en Paraguay a través de un software de control, que es nuestro, y accedemos para ver si hay algún problema que podamos solucionar, que puede ser de mantenimiento preventivo”.
Por eso, ya no es la misma empresa que se fundó hace 12 años: “ese trabajo hace que la infraestructura que se creó en automatización dentro de la empresa, haya crecido en los últimos tiempos. Pasamos de ser una empresa que suministraba trabajos de metalúrgica, a ser una empresa que suministra sistemas. La metalúrgica, con la fabricación, se hace en Paysandú, pero el desarrollo de sistemas, que antes se compraba, hoy se desarrolla también acá en Paysandú y se aplica en otros lados”. Tan es así, que “tenemos sistemas en silos de granos en Paraguay, hemos vendido el software de automatización en Bolivia, como en Montevideo o Algorta”.
Para llegar a este punto, “implicó una inversión en recursos humanos, en servidores, en tecnología. Ademas somos representantes de Mettler-Toledo, una empresa suizo-americana que tiene un sistema creado en Estados Unidos, y basado en él desarrollamos todas las herramientas. También tenemos alianzas con empresas de software en Paysandú, por ejemplo el sistema Magna, que utilizamos mucho en distintos clientes. De esta manera creamos la posibilidad de desarrollar trabajo localmente”.
Técnicos de UTEC y de la UTU
Sobre como fue llevar a la metalúrgica al ambiente de los programas informáticos, y cómo conformaron el equipo, Russi afirmó que “no es fácil. Con las alianzas que tenemos, esos recursos ya están en empresas, pero nosotros tenemos nuestros propios recursos humanos para nuestros sistemas de automatización. Pero conseguir gente capacitada para desarrollar sistemas no es una tarea sencilla. Pero en Paysandú por suerte hay donde buscar, y recurrimos mucho a la Universidad Tecnológica (UTEC), hemos contratado gente que estudió allí, y también de la UTU. Hay gente joven que estudia tecnología, hay carreras como Agrónica, carreras de automatización, ingenieros tecnológicos. Y estamos muy relacionados con la industria forestal y la agro industria, por lo que además de requerir trabajo en sistemas acá (en la ciudad) también requiere trabajo en campo. Porque esos instrumentos de control, tienen que estar instalados, y por suerte hemos encontrado gente capacitada. Y hay muchas empresas del sector que aplican tecnología”.
“Los últimos técnicos que contratamos son todos de UTEC”, aseguró Abel Rochón, y es una base de gente joven, comprometida y apostamos a ellos. Y nos ha ido bien, es una de las bases de la empresa y va en línea de haber pasado de la metalúrgica a la atención de sistemas”.
Dijo que “hay que mantener un brazo metalúrgico, porque siempre hay alguna base de adaptación, de montajes que es bueno tener, pero después toda la parte de mantenimiento e instalación de los sistemas, que se ha desarrollado últimamente, y con estos muchachos hemos andado muy bien”.
Potenciar los recursos y herramientas
Los empresarios tienen una visión de largo plazo. “Encaramos un proceso de certificación ISO 9001 en la parte de sistemas de pesaje, también tenemos detectores de metal y medición de humedad del grano, y la atención del servicio en ese proceso requiere una especialización en sistemas. Se trata de lograr esa certificación y potenciar los recursos y las herramientas, porque el futuro para nosotros es lograr una atención inmediata a un cliente en cualquier punto, que ese cliente pueda instalar la tecnología que le sugerimos para poder atenderlo en un plazo rápido”, y explicó que “el requerimiento de las grandes industrias que se están instalando en el país es la atención 24/7, pero tener los recursos humanos disponibles todo ese tiempo es prácticamente imposible, o muy costoso, entonces eso se sustituye con tecnología en la atención primaria”.
“Después, el segundo paso, es la atención en el lugar. Por ejemplo, una balanza de camiones tiene determinada cantidad de sensores. Hay algunos de ellos que podemos verificar en línea y corregirlos, por ejemplo un sensor de posicionamiento, y el cliente puede seguir trabajando. El segundo paso es que el técnico va al lugar y verifica ese sensor de posicionamiento, y de ser necesario lo repara, pero el cliente en ese plazo no dejó de trabajar, que ese es nuestro objetivo, que la industria no deje de trabajar. Lograr el menor tiempo de inactividad, que es lo que requiere la industria”.
Que las plantas no paren de trabajar
Rochón puso como ejemplo que “muchas veces la primera línea de contención nos sirve que esté en el lugar. Por ejemplo, solucionamos un problema en Agraciada donde el equipo nos daba el código de error, que es certero, y con ese dato fueron, lo limpiaron y el equipo quedó andando, la planta siguió recibiendo la zafra con una demora de menos de 20 minutos, con atención on line. Poder llegar a ese tipo de situaciones, que los equipos den información para que, a través de video llamadas y con toda la tecnología que tenemos disponible, podamos realizar muchas actuaciones a distancia, que generan que la persona pueda tener rápidamente el equipo nuevamente operativo, o si hay que ir al lugar hacerlo con un diagnóstico específico para poner el equipo en funcionamiento lo más rápido posible”.
Russi destacó que “hoy hay una tecnología en balanzas, camiones, sembradoras o cosechadoras, que emite mensajes que están en la nube, y lo que hacemos es saber cómo manejar esa información, que lo hacemos mediante el software y nosotros lo parametrizamos en Uruguay, trabajamos sobre eso”.
Por eso, “nosotros estamos muy vinculados con el transporte y la logística, que van de la mano, porque un camión que tenga que esperar en una planta porque la balanza no tiene el funcionamiento correcto, es un camión parado, y pierde la planta, el camión y todos, y se afecta toda la cadena logística. Por eso la industria 4.0 trata de asegurar la operatividad de los equipos”.
“La tecnología ya está instalada”
Sobre cómo dieron el salto de ser solamente una empresa metalúrgica a llegar a brindar, además, servicios en red, y qué reacción tuvieron los clientes, Russi dijo que “los clientes lo que mas valoran es no parar”, y Rochón afirmó que “los clientes están acostumbrados, porque la tecnología ya está instalada hasta en un tractor de campo, está en la primer línea”, y que “todos nos acostumbramos al manejo de la tecnología”.
“Se evoluciona, hace 10 años no hacíamos lo que ahora con un celular. Y los sistemas han facilitado mucho, porque hoy tenemos algunos que funcionan a través de lectoras de antenas. La información que tiene que ingresar un camión a la entrada de una planta es mínima, ya hay lectores que leen la antena, lo único que debe hacer el camionero es pasar la tarjeta frente a un lector y prácticamente el sistema actúa en forma autónoma. Entonces es mucho menos lo que la persona tiene que interactuar con los sistemas, que son cada vez más autónomos.”
Comparó ese sistema con “los telepeajes, que es la misma tecnología que se está aplicando cada vez más, porque es la optimización de recursos”, y destacó que no necesariamente representa menos personal trabajando, sino que “tenemos clientes que aprovechan ese recurso humano en otras tareas, y el ingreso a la automatización tiene un cambio positivo, porque ese recurso humano que parece que queda afuera por la automatización, es capacitado y especializado en otra cosa, por lo que tiene una nueva oportunidad”.
00